Featured Stories, MIT | February 4, 2013
The Real Reasons to Build an Oil-Sensing Robot
By Genevieve Wanucha
It was December of 2011 on one of those exhausting days during finals. The MIT Marine Robotics Team was having an especially rocky time. The team had just lost their founder and leader, Matt Gildner (MS ’12), to graduate studies. “The project wasn’t going anywhere at that point,” says Jacqueline Sly (’14), then a sophomore. She mentioned to the team’s faculty mentor, MIT mechanical engineering professor Franz Hover, that she might just leave the team. “What can I do to keep you around?” he responded.
Sly never did leave. She became the group’s captain instead. The Edgerton Center-sponsored team braved their growing pains, remaining in the corner of the MIT Center for Ocean Engineering that’s created such industry buzzwords as the Robo-Tuna and Bluefin Robotics Company. It should go without saying that this undergraduate team is not geared toward contrived team competitions but real-world problems.
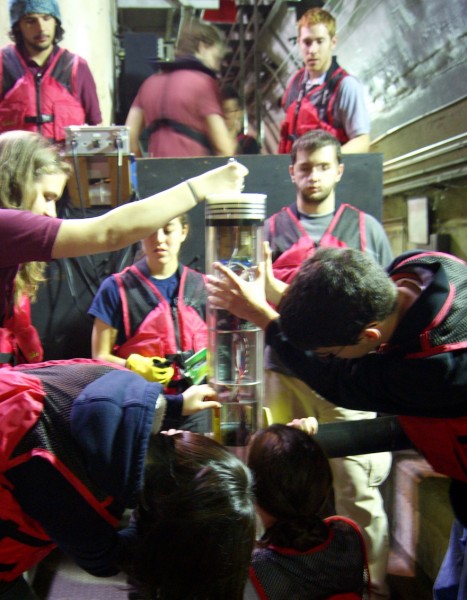
The team notes that just in the last couple months, momentum in the group has surged. The reason? “The thing is, we built a glider,” says MIT junior Tommy Moriarty (’14), a longtime team member. He’s talking about the autonomous underwater vehicle (AUV) they designed and built over the past year. They recently tested the robot’s behavior in Ketchikan, Alaska, a successful run that’s gained notice on campus.
The path to Alaska was a roller coaster experience for these 15 students, filled with lessons unobtainable in the classroom. Miscalculations led to the ordering of parts 4 times too big, and underestimations of aluminum strength resulted in a broken battery carriage. Upon arriving in Alaska, the team realized with agony that they had forgotten the wing mounts for the glider. But they had brought some raw materials. Minutes later, they were cutting and drilling new mounts on the floor of their hotel bathroom.
“There’s not much you can do to get that experience,” says Moriarty, “to be somewhere where you just have to be creative and fix problems—you only get that when it happens to you.” Those moments of on-site problem solving are the reason why the team knows what it will take to design, build, and test another iteration destined for a much larger mission.
These days, the multinational energy corporation Chevron is funding these undergrads to design marine robotic solutions to oil rig safety issues in the Gulf of Mexico. While Chevron’s main goal is to support the next generation of ocean-minded engineers, they’ve also set their sights on the Marine Robotics Team’s next robot design because of its low-cost, high-function potential. Meanwhile, the students are gaining something far beyond anything money can buy.
***
An AUV glider has a long cylindrical body with a pointed nose and side wings; it looks a bit like a torpedo (a slightly inconvenient fact when the team must ask the TSA to let them strap it into a plane seat). The glider runs on a buoyancy engine, which controls the vehicle’s up-down movement in the water. The wings act to convert vertical action to horizontal, passively propelling the glider forward through water in an up-down sawtooth pattern. Sly explains it herself in this footage from Alaska.
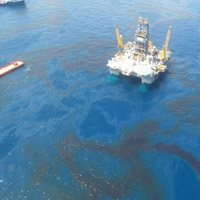
It’s the attached sensors that turn an AUV glider into a crude oil hunter. In fact, the Deep Water Horizon disaster presented the world an urgent opportunity to use gliders for this very purpose. Engineers at the Navy, the Massachusetts-based iRobot, and Woods Hole Oceanographic Institution among six other universities, deployed AUV gliders during this catastrophe to monitor subsurface oil by tracking the dispersal of hydrocarbons through ocean currents.
The Marine Robotics Team (MRT) is pushing this oil sensing application a bit further. In contrast to the industry’s robots that are deployed during or after emergencies, the future MRT gliders will act as agents of oil spill prevention. “What we are seeing,” says Sly, “is that when a leak does happen, there is often a small amount of oil in the water before a massive plume at the surface.” In her vision of the everyday operation, two MRT gliders would continually move in a spiral pattern around each underwater rig in the Gulf, monitoring the water for hints of oil. At each journey to the surface, the sensors send their data to humans via satellite.
Able to monitor real-time data, engineers would be positioned to investigate potential spills in time to make a difference. “It’s a more responsible way to run any kind of oil rig operation, and it’s looking like the right way to do it,” says Sly.
The major draw for Chevron is that the cost of the MRT gliders (approx. $5,000, not counting oil sensors) is a pinprick compared to the $100,000 and up that industry gliders exact. And besides being good business for the company, the economics is simply good for oil spill prevention. In short, more robots, whole fleets of them, could be deployed to monitor continually. Most importantly, the gliders would be expendable. Chevron wouldn’t need to pay for salvage missions for runaway robots, which will be tagged ‘This is Not a Weapon’ for when one washes up on a beach.
***
John J. Leonard, Professor of Mechanical and Ocean Engineering at MIT, knows what these MIT students are in for. From his daily experience addressing problems in AUV navigation, he thinks the big challenge for team, over the long haul, will be “robustness,” or how reliably a system can work over long time spans. “It’s one thing if it works in the lab, or the first time you deploy it,” he says. “But having something that works day in and day out for long-term operations is the hard part.” The team takes Leonard’s point to heart; it’s why they stay late in the lab (“Sometimes their best ideas come at 2 AM,” says Hover) building a more “robust” engine.
In Alaska, the team ran into a couple of problems with their engine. The seals on the motor-driven piston sometimes popped leaks, letting water in to throw off the robot’s buoyancy. Several members, including sophomores Sarah Brennan (’15) and Jaya Narain (’15), are ready to revamp the system. This new kind of buoyancy engine uses a pump to move fluid from an exterior bladder to an interior reservoir. It’s more robust than a piston system. Moriarty describes it best: “We’re trying to see how we can make it dive better, dive deeper. Better with less problems, less moving parts.”
***
When Sly opens the door to the “Marine Robotics” workroom in Building N52, the rich hydrocarbon aroma of crude oil hits you. A big blue plastic barrel holds a black pool of water and crude oil, the leftovers from one of the team’s experiments. On the desk, next to an array of robot appendages and a “Frankenstein” glider, sits a puckered gasoline can of pure crude oil. This is where the oil-sensing component of their project develops.
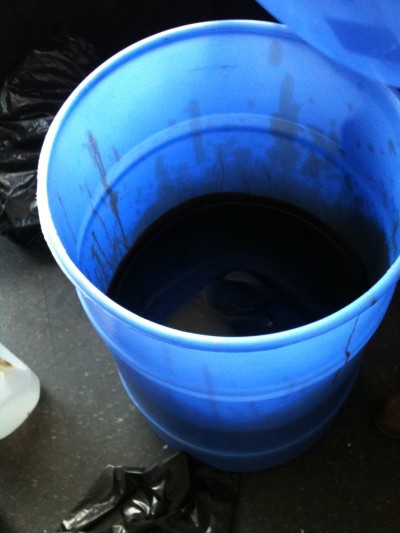
They must investigate exactly how sensors detect oil in water. In beakers, they mix crude oil and water in certain concentrations by weight and then collect data with a sensor called a fluorometer. This fluorometer is specifically “tuned” to detect crude oil; it sends a wavelength of light that fluoresces in particles of crude oil. They are analyzing the data collected from sensors sitting in fresh water, salty water, water with small amounts of crude oil, or full-on crude.
These experiments have already produced some interesting findings, both unexpected and critical to real-world data interpretation. The team discovered that even in identical concentrations of oil, the sensor was giving varying results from one test trial to another. It really worried them—until they realized that the concentration measurements are temperature dependent, presenting as radically different readings in, for example, 30 ˚C and 50 ˚C liquid. “Stuff like that is really interesting to find,” says Sly. “It’s something we have to reverse engineer.”
***
In the grand scheme of the marine robot industry, the students are still just taking baby steps toward a real application. They are, after all, still growing into engineers. “I would not say we are going to be competitive with industry players anytime soon,” says Hover, “but you may well see some innovations in stuff that’s not currently present in the general glider community.”

Yet, it’s looking like one of those innovations will come sooner than later. It turns out the Gulf of Mexico Loop Current, one of the fastest currents in the Atlantic Ocean, puts significant stress on oil rig platforms. And Chevron needs to design a more dynamic rig, one that may be able to adapt to the seasons and better withstand the Loop’s force. However, the temperature-dependent behavior of the Loop is poorly understood. The team’s main contact at Chevon recently asked if the MRT’s glider platform, equipped with inexpensive temperature sensors, could be launched en mass into the Gulf to collect water temperature data, valuable to oceanographers and Chevron engineers alike.
All that aside, this project has a far greater meaning for the Marine Robotics Team than the chance to interact with industry. As the past year illustrated, participating in the Marine Robotics Team gives students the unique chance to create advanced technology under only hands-off faculty guidance. The resulting student-made, student-designed technology provides a sense of ownership of an ocean engineering future.
Sly plans to pull back from the group after their next mission to Houston this summer. She wants to give more responsibility to younger underclassmen so they will have enough knowledge to run the project when she eventually departs for graduate school. “I don’t want them to have to make that crucial last minute decision of ‘do I stick with it or not?’ ‘does it die or not?’,” she says. “It’s great to see a robot come out of it, but it’s even better to see a team of people that’s renewed every year.”